This article will compare the advantages and disadvantages to find the best solution for reliable level measurement.
Radar technology is increasingly being considered the optimal approach for level measurement. However, this does not apply to every application. Non Contact Level Transmitter
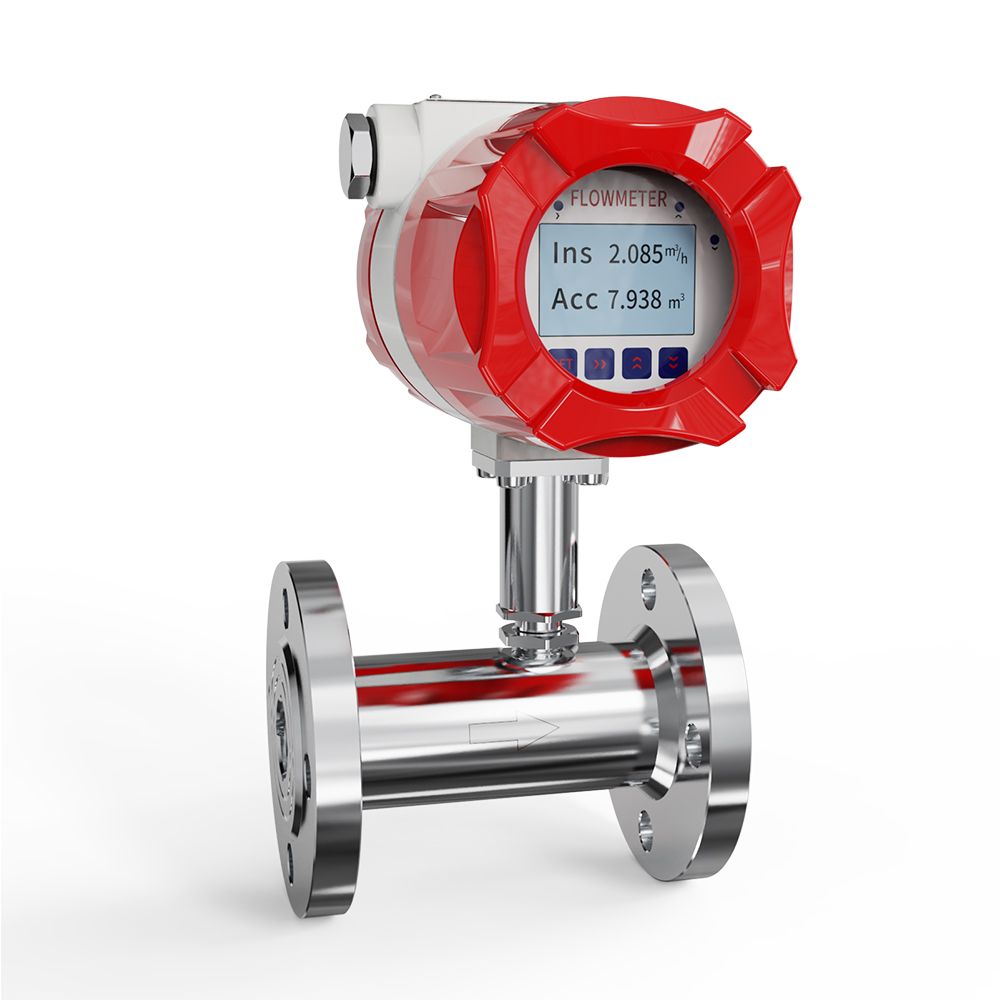
Despite the significant advancements in performance, accuracy, and cost-effectiveness of radar sensors, they cannot be universally applied and should not be treated as such.
While radar is versatile, there are specific scenarios where ultrasonic-level technology is more suitable.
Prioritizing a tailored solution rather than a generic approach in level measurement is crucial to maintain safety, performance, and overall product quality.
In this article, Scott Peterson, a level expert from Endress+Hauser, delves into the disparities and advantages of ultrasonic and radar technologies and the respective applications where each should be considered.
Ultrasonic level sensors employ the Time of Flight (ToF) principle, utilizing an ultrasonic transducer to generate a mechanical sound pulse that travels through the air toward the process.
Upon encountering the process surface, the pulse reflects back to the transducer.
The transmitter acts as a sophisticated timer, measuring the round-trip time of the pulse's journey to and from the process. This duration directly corresponds to the distance between the gauge and the process surface.
Image Credit: Endress+Hauser Ltd.
Radar level sensors, on the other hand, also rely on the ToF principle but operate with electromagnetic waves rather than sound waves.
Unlike sound waves, which reflect based on density variations, microwaves reflect based on changes in impedance caused by the transition from a low dielectric medium (air) to a higher dielectric constant of the process medium.
The ultrasonic method has proven to be a cost-effective and reliable solution for measuring the level of liquids and bulk solids. It boasts several advantages, including easy planning and installation, swift and secure setup, a prolonged lifespan, and reduced maintenance expenses.
Since ultrasonic measurements are not dependent on the dielectric constant for reflection, they are suitable for applications involving process media with low dielectric constants (<1.5), except for hydrocarbons. Ultrasonic technology is well-suited for open channel flow measurement and use with weirs or flumes.
The radar method provides the following advantages:
The dielectric constant serves as the primary limitation for radar systems. Materials with low dielectric constants may lack sufficient impedance variation to induce a reflection. Consequently, microwave energy passes through these materials, reflecting off the bottom of the vessel.
Some examples of materials with excessively low dielectric constants for free space radar encompass dry sawdust, wood chips, white cement, and numerous plastic pellets. In such scenarios, ultrasonic transmitters prove useful for measurements where radar transmitters fall short.
Certain users have transitioned from ultrasonic sensors due to past challenges from dust accumulation or condensation on the transducer's faceplate. Nonetheless, employing an ultrasonic sensor with automatic self-cleaning, such as the Endress+Hauser Prosonic FDU91, eradicates such failures.
Prosonic FDU91 PP. Image Credit: Endress+Hauser Ltd.
Since microwaves operate electromagnetically without dependence on air as a transmission medium, radar finds practical applications in vacuum environments or when other gases are in empty spaces.
Radar technology remains safe and reliable even amidst extreme process conditions involving pressure, temperature, and vapors. Typical applications include storage tanks, particularly those housing corrosive or aggressive media, and high-precision tank gauging requirements.
Ultrasonic sensors can effectively address challenges faced by end-users in confined spaces. They are an ideal choice for such installations due to their compact size and the ability to mount them directly on the ceiling.
In flooding scenarios, an ultrasonic sensor, when used in conjunction with a flooding protection tube, can ensure accurate measurements even when submerged underwater.
For outdoor setups where temperatures can drop below freezing, ultrasonic sensors equipped with built-in heaters prevent ice formation on the device, guaranteeing reliable measurements throughout the year.
Unlike radar, which can be affected by icing due to the high dielectric constant of ice, ultrasonic sensors overcome this issue by maintaining a consistent radar signal reaching the product surface for level measurement.
Radar technology, conversely, proves valuable when end users encounter challenges, such as vacuum conditions, temperature fluctuations, air turbulence, or changes in the vapor space, such as gas layers.
As an electromagnetic wave, radar does not face the limitations of mechanical waves seen in ultrasonic technology.
To cater to diverse ultrasonic level measurement requirements, Endress+Hauser provides an extensive range of devices under the Prosonic product line, including 12 ultrasonic Time-of-Flight (ToF) sensors and two powerful transmitters.
These products remain unaffected by dielectric constant, density, humidity, dust buildup, or condensation.
Among the Prosonic devices, the FMU90 ultrasonic transmitter, in combination with an FDU9X transducer, stands out as an excellent choice for various applications.
It has additional features like totalization, data logging, differential measurement, pump control, and open channel flow tables. Moreover, the FMU90 is also available in a cost-effective two-channel model, reducing overall hardware expenses.
Ultrasonic FMU90 transmitter. Image Credit: Endress+Hauser Ltd.
Ultrasonic measurement Time-of-Flight Prosonic FDU95. Image Credit: Endress+Hauser Ltd.
For radar-based level measurement, Endress+Hauser presents a comprehensive range of products suitable for solids and liquids.
Starting with the compact Micropilot FMR10 and FMR20, which offer an excellent price/performance ratio, the product line progresses to the FMR5x models, providing options at 6 GHz and 26 GHz, along with advanced diagnostics and multi-echo tracking capability.
At the top tier, the FMR6x models offer outstanding 80GHz performance for solids and liquids, ensuring precise and reliable measurements.
Micropilot FMR10 and FMR20 with tablet. Image Credit: Endress+Hauser Ltd.
This information has been sourced, reviewed and adapted from materials provided by Endress+Hauser Ltd.
For more information on this source, please visit Endress+Hauser Ltd.
Please use one of the following formats to cite this article in your essay, paper or report:
Endress+Hauser Ltd.. (2023, June 06). Comparing Radar vs. Ultrasonic Sensors. AZoSensors. Retrieved on January 22, 2024 from https://www.azosensors.com/article.aspx?ArticleID=2817.
Endress+Hauser Ltd.. "Comparing Radar vs. Ultrasonic Sensors". AZoSensors. 22 January 2024. <https://www.azosensors.com/article.aspx?ArticleID=2817>.
Endress+Hauser Ltd.. "Comparing Radar vs. Ultrasonic Sensors". AZoSensors. https://www.azosensors.com/article.aspx?ArticleID=2817. (accessed January 22, 2024).
Endress+Hauser Ltd.. 2023. Comparing Radar vs. Ultrasonic Sensors. AZoSensors, viewed 22 January 2024, https://www.azosensors.com/article.aspx?ArticleID=2817.
Do you have a question you'd like to ask regarding this article?
AZoSensors.com - An AZoNetwork Site
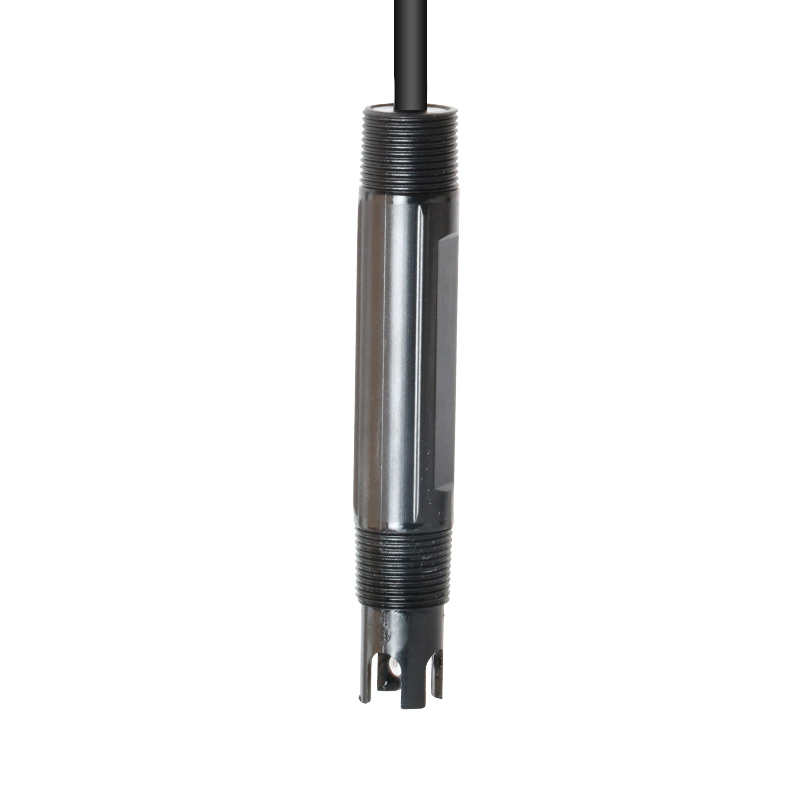
Level Owned and operated by AZoNetwork, © 2000-2024