There is a perpetual squealing and growling noise coming from the motor. This worrying rumbling noise increases slowly every day at a microscopic level. This is the symptom of bearings starting to erode. Motor experts have stated that 50% of motor failures are caused by bearing defects.
IMAGE 2: AC motor with high PWM signal Variable Frequency Phase Converter
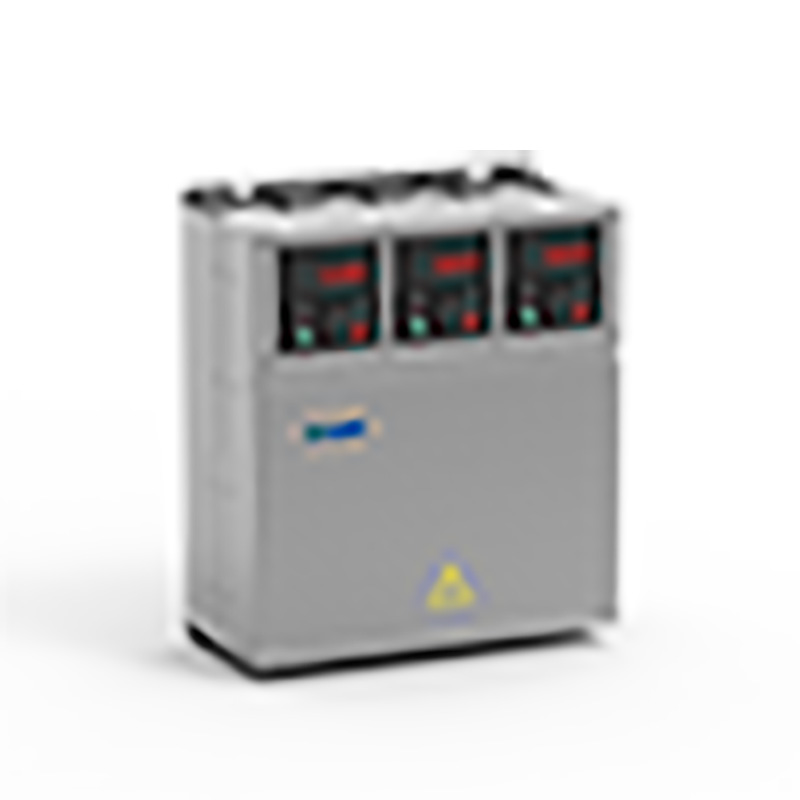
The primary causes of bearing failures (80%) are mechanical, of which:
These issues can be managed with proper care and an effective maintenance plan. There are other sources of bearing issues, such as variable frequency drives (VFDs), induced bearing currents (which require some action to avoid premature aging), and motor failure.
Since they were first introduced over 40 years ago, VFDs have had a dramatic impact on the industry. Through the use of power electronics, they enable precise control over motor torque and speed, matching the delivered movement with the exact need. Users enjoy energy savings and experience less stress on the motor transmission/drivetrain as a result.
IMAGE 3: AC motor with high PWM signal
Historically, the benefits of VFD technology have come at a cost. Non-state-of-the-art VFDs come with drawbacks such as harmonics, electromagnetic interference (EMI), delta voltage over delta time (dv/dt), requiring the use of bulky filters and limiting cable lengths.
The less understood phenomena in many applications are the electric currents traveling through the motor bearings, commonly named bearing currents. Bearing currents are the root cause of pitting, fluting and frosting of the ball bearings and bearing races.
Electrical motor bearings are designed for 100,000 hours of operation. That is over 11 years of continual daily usage. When bearings fail (50% of motor failures) the consequence is not just the cost of repair.
IMAGE 4: Part of this current flows between the inner race and the outer race of the bearings, causing heat in the lubricant.
The first consequence is unplanned maintenance and the cost of lost production. There is also the potential damage to mechanical loads and couplings attached to the motor’s shaft. This can occur as a direct result of either bearing failure or during the reactive maintenance performed after the failure.
With respect to reactive maintenance, several studies have demonstrated that 28% of workers are more likely to have an accident at work while performing reactive maintenance over proactive maintenance.
The production downtime associated with unplanned, reactive maintenance has negative consequences including loss of production, missed deadlines, loss of revenue, increased staffing costs to make up lost production and the cost of the repairs themselves.
Common mode voltage is defined as the voltage across the neutral point of the motor and the system grounding. The voltage from neutral to ground (common-mode voltage) can be calculated in terms of phase to ground voltage as the averaged sum of the three voltages.
IMAGE 5: These capacitive discharge currents can cause fretting of the bearing and raceways and produce temperatures high enough to melt the bearing steel and cause pitting.
For a three-phase motor that is powered with a three-phase voltage signal, when the system is well-balanced, these three voltage signals are theoretically the same amplitude with a phase shift of 120 degrees. In this scenario, a balanced alternating current (AC) motor must be driven by a balanced three-phase AC source and the common mode voltage will be zero.
When a motor is driven by an ordinary VFD, the fast switching of the insulated-gate bipolar transistors (IGBTs) generates three high frequency pulse-width-modulation (PWM) signals. Being unbalanced, they are the source of a nonzero voltage (common mode voltage) difference between the neutral point of the motor and the system grounding.
The structure of the AC motor, combined with this high-frequency PWM signal, make the motor stray capacitances (also known as parasitic capacitances) non-negligible.
The stray capacitance circuit is the source of a shaft voltage when the motor is spinning and the common mode voltage is non-null. The high frequency of the PWM can make this shaft voltage generate sparks and arcing through the bearing lubricant, which results in pitting and fluting on the bearing races.
IMAGE 6: Shaft currents flowing through the bearings alter the chemical properties of lubricating oil.
When the motor speed is low, the inner race and outer race of the bearings are in physical contact with the ball bearings. In this case, the bearings parasitic capacitance does not exist and there is no shaft voltage.
There are different types of currents which are harmful to motor bearings, or that may even disrupt motors.
Coming from the high-frequency PWM signal, the common mode voltage is also a source of fast transient voltage (high dV/dt). This high dV/dt creates current pulses between the rotor and the stator windings via the stray capacitance. Part of this current flows between the inner race and the outer race of the bearings, causing heat in the lubricant.
Electric discharge machining (EDM) bearing currents
Common mode voltage generates an electric charge, stored in the parasitic capacitance between the rotor and the stator. When this charge becomes high, it breaks the dielectric insulation and is discharged through the insulation of the bearing, creating what is called EDM bearing currents. These capacitive discharge currents can cause fretting of the bearing and raceways and produce temperatures high enough to melt the bearing steel and cause pitting.
IMAGE 7: In this case, the bearings’ parasitic capacitance does not exist and there is no shaft voltage.
If the motor frame is poorly grounded and the motor is connected to a mechanical load that has a proper grounding (low impedance), the common mode current flows through the shaft reaching for the lower impedance to the grounding. Currents traveling through the shaft are named shaft currents. Shaft currents flowing through the bearings alter the chemical properties of lubricating oil, impacting the shaft with the mechanical wear produced by the buildup of metallic debris.
Best-practice installation rules must be applied to contribute to the bearing current mitigation.
Typical mitigation to prevent bearing currents and the damage they cause is to interrupt or block the current’s path.
A common mode choke is installed between the VFD and the motor to reduce peak currents from the above-described phenomena to levels that are harmless to the motor.
Improve grounding from the motor to the drive and from the motor to its mechanical load by correctly using bonding straps.
Use insulated coupling between the motor shaft and its mechanical load.
Add a shaft grounding ring on the motor drive end and an insulated bearing on the nondrive end.
However, these mitigation measures do not eliminate common mode voltage, they simply reduce its impact. Mitigating measures must be part of the preventive maintenance plan to ensure their effectiveness over time.
By implementing the latest generation of electronic power components (silicon carbide [SiC] transistors), with innovative and patented algorithms and optimized integrated filters, clean power VFDs provide AC motors with a clean and pure sine wave.
When a clean sine wave voltage is applied to a motor, the common mode voltage is virtually zero. No shaft voltage is generated and no common mode current flows at any point in the cycle. Therefore, bearing current’s root cause does not exist when using a clean power VFD, and premature aging of the motor is not a concern. However, there is always potential bearing and shaft currents for sine wave driven motors due to lack of motor symmetry from its electrical design.
Bearing and shaft currents can always flow through conductive materials like motor shafts, frames, bearing races and bearing balls. They are often called circulating currents. Some motor manufacturers design motors with an insulated bearing. These designs are created to interrupt the closed path of circulating currents through the bearings to the grounded motor frame.
To prevent the most frequent cause of motor failure is to correctly maintain the bearings and to avoid the issues stemming from common mode voltage. Insulating the bearings with ceramic or other non-conductive materials and installation of shaft grounding rings may be helpful. However, those are just band-aid solutions and do not fix the issue’s root cause.
SKF, Bearing failures. skf.com/binaries/pub12/images/0901d1968064c148-bearing-failures---14219_2-en_tcm_12-297619.pdf
Dean Payn- for BDS bearings - What causes bearing failures and preventive measures you need to know. bdsbearing.com/blog/bearing-failures
Ciprian Radu - for Bearing News -The Most Common Causes of Bearing Failure and the Importance of Bearing Lubrication. bearing-news.com/the-most-common-causes-of-bearing-failure-and-the-importance-of-bearing-lubrication/
Rockwell Automation - Installation Considerations for IGBT AC Drives. literature.rockwellautomation.com/idc/groups/literature/documents/wp/drives-wp019_-en-p.pdf
Rockwell Automation- White Paper on maintenance.org - Inverter Driven Induction Motors Shaft and Bearing Current Solutions.

Inverter Fed Induction Motor Damien Herwegh is the offer manager for SmartD Technologies, with more than 25 years of experience in the automation industry focused on marketing for the user’s experience understanding. For more information, visit smartd.tech.