Controlling the water is critical when using a continuous concrete mixer on your next concrete job under 5 yards.
Concrete contractors working a job too small for a ready mix truck have a short list of options to prep concrete. Top of the list is the tool and wheelbarrow. While tried and true, it’s the choice with the most manual labor. There’s the mobility of the drill and paddle— made even more convenient with modern cordless battery-powered tools. And, of course, the ever-familiar standard barrel or mortar mixer with a ribbon. Concrete Mixer
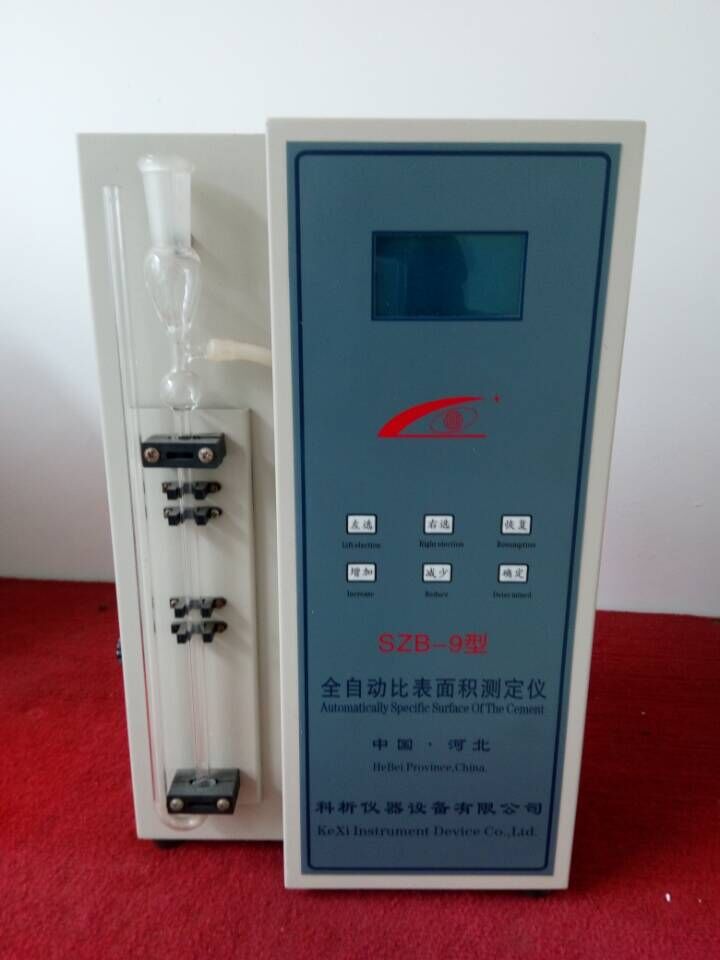
The thread that connects these solutions together: batching (and intense labor). Consider both wheelbarrow and barrel a batch mixer, forcing contractors to add the right amount of water and mix until ready. Place and mix again.
Continuous or in-line mixers, on the other hand, provide a steady action and supply of concrete for the job. However, the traditional design of these machines has been typically aimed at larger projects like dams and high-rise buildings, etc.
MudMixer MudMixer took this idea and applied it towards smaller and repair projects— the projects that fall below truck delivery minimums. Their design places a hopper directly above an auger which pushes material into a small chute. Adjustable nozzles add water. The movement mixes the material and if everything is set up correct, the concrete pours out ready. Designed to work with bagged concrete, as long as the hopper has material, concrete will continue. This is not a pump. There is no pressurized hose. Picture a volumetric truck but on a much – much - smaller scale.
And a whole lot more lightweight.
They’ve basically taken the wheelbarrow out of the equation. “With a traditional barrel mixer, [contractors] mix, then dump it in a wheelbarrow, and then you take the wheelbarrow up to your forms, dump it in there,” says Peyton Maddox, marketing director at MudMixer. “We put the mixer on a wheelbarrow frame … basically, you walk it right up to your forms and leave the wheelbarrow at home.”
On a large-scale, ready-mix plants can provide some level of quality control by controlling measurements to ensure the required mix specifications are met. For this size of a continuous mixer, instead, experts say it’s better to keep the mix simple. It’s vital to not overdose, keep constantly feeding the dry premix, and keep a fair constant supply of water.
PRO TIP Keep the hopper at least halfway full to ensure a consistent mix throughout the whole pour.
Not aimed at replacing the ready-mix truck, the team wanted to develop a solution for smaller jobs. “You’re not going to pour 20 yards with a MudMixer, ” notes Maddox. But, he says, it puts contractors back in charge of their own time and avoid a minimum load charge.
Compare the cost ordering the yards of concrete vs mixing it on-site; think about 2 to 4 yards at one time. Also consider accessibility situations of the site. Perhaps it can only be reached by boat, the truck won’t fit, or delivery wait-time doesn't match the schedule. If you can’t get a ready-mix truck for a larger pour, MudMixer recommends placing 3 to 4 yards at a time in sections until the project is done.
Maddox sees the machine’s unique design is what sets them apart. It’s something the world hasn’t seen regarding bag concrete projects. MudMixer
“[Continuous] mixers have a hopper,” says Dave Wingard, group leader at QUIKRETE. “Depending on how much you put in, as long as you keep the same level of material constantly the bags will come out consistent.” The trick with continuous mixers is ensuring time enough for the water to blend.
Without automated systems like Verifi by GCP or ACCU-POUR from Cemen Tech Inc., water flow will need to be set and controlled manually. The only way to find that quality – workable – concrete requires two critical parameters to be consistent: keep feeding the hopper and control the water.
Addressing this, MudMixer requires a pressured water source – not gravity fed. The company recommends 30 psi minimum. A pair of adjustable water nozzles spray the amount needed controlled by dial valve with values from 0 to 100 (0 is closed; 100 is full open). The machine’s switch powers both the 36-in. auger and solenoid – turning both off at once. They recommend starting the dial at 50.
PRO TIP Contractors can find a water-range on universal bags. Even with barrel-style or paddle mixing, contractors do not always need to use the max limit. A good starting point, instead, is the front end or the middle. This allows time to adjust.
This control allows contractors to make the mix as they need. If reliant on, say, a residential garden hose – make sure to watch the mix carefully. “Every water pressure is different,” notes Maddox. “If someone is running a load of laundry and pulling some water, [contractors] will have to dial up a little. They have full reins on setting that water dial. Once you have it set, your mix is going to be consistent the whole time.”
It should take about 10-15 seconds after starting to know what the mix is going to be. It’s recommended to make small adjustments until the mix is to the consistency needed. “Once you get it set, you just drop bags,” says Maddox. Contractors will find an arched bar set within the hopper to help split bags.
Since the mix doesn’t remain in the hopper for a significant amount of time, a continuous mixer on this scale may not allow time enough to agitate additions like water reducers to be fully dispersed. “The simpler the mix, the better for the system,” suggests Bing Tian, director of R&D, at QUIKRETE. Think premixed and straightforward. For example, QUIKRETE’s standard yellow-bag mix.
Look through the technical data sheets on your bags to ensure it’ll mix well and has everything needed for the job. Fiber reinforcement or any additives need to be pre-mixed in the dry material before going into the hopper.
It’s making sure to use the right bag for the project and making sure you're using the right mixer for the job at hand.
Peyton Maddox worked in construction as a pool builder for 2.5 years before joining the team as marketing director for MudMixer. Mixing concrete by hand and a wheelbarrow, he saw the need and was blown away once he gave it a shot— calling it the best idea he’d ever seen. MudMixer
It took the team behind MudMixer two years to finalize, changing one thing after another until it was right. Wanting to keep it simple, they eliminated as many variables as possible except controlling water flow. The electric 1.6-amp motor will run at 118 RPM regardless of where the contractor sets the water dial. At this speed, MudMixer will mix an 80-lb. bag in about 70 seconds.
As they continued to work on the machine’s design, they added a 330-degree swivel, flat-free tires, and eventually a hopper extension to increase the capacity from 120 lbs. to 300 lbs. (extension sold separately).
“We’re about to release another accessory called the chute extension,” says Maddox. “It goes on the end of the chute…an arm that provides more reach and more accuracy.” Once available, it’ll add another 18 in. of reach along with 15-, 25-, and 35-degree angles. The extension is scheduled to be ready in Q3 of 2023. MudMixer
The team also added a T valve at the water intake allowing a secondary hose and spray nozzle to help clean-up. Further aiding this, the company provides two recommendations on its website— a concrete dissolver and concrete shield.
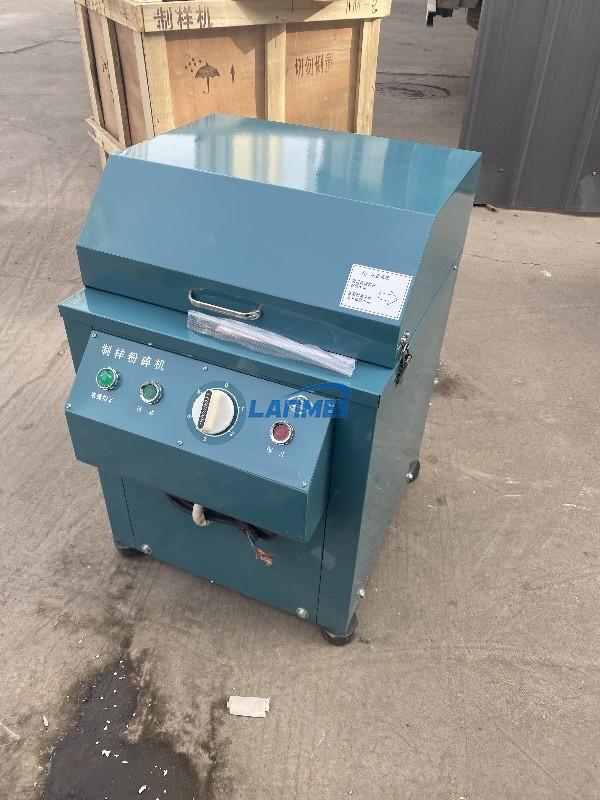
Laminar Flow Bench The company started with a small team of about 4 people and are steadily growing. Recently, they’ve tripled their manufacturing output with a nationwide dealer network and rental companies.